Spending much time staring at the stock and M-Unit wiring diagrams. Planning a harness takes a lot of thought before you even touch wire and that goes double for an M-Unit because it's so different. One of the Revival Cycles guys said, "If a stock headlight switch functions essentially like a household light switch, the same physical switch in an M-Unit setup functions like the enter key on the keyboard of the PC you're on right now." And that's really the best description.
After studying and studying those diagrams and watching and rewatching every YouTube video on M-Unit and Harley wiring stuff I could find I set up a bench testing station to check connections before I started putting wire back on the bike.
I scanned in the stock diagram and used a free online image editing program named Gimp to cut it up into pieces. I got rid of what I didn't need and kept what I did. I created "groups" for the various circuits, Left grip switches, right grip switches, left turn signals, right turn signals and so on. I organized it into "layers" (anyone who has worked with Photoshop or other similar image editing software will be familiar with layers) so I could make changes without affecting other groups. This also makes it easy to turn visibility off and on and move groups around the page individually.
I'm planning on posting the finished diagram, but not until after everything is installed and tested. I don't want to put bad info out there. Also, even though some wire colors will be the same, this diagram will bear no resemblance to the stock one at all with regards to how things flow so it will really only be useful if you are installing an M-Unit.
I have had a couple times where I got stuck on a circuit and had to shoot an email to Revival Cycles tech line and get bailed out. Jeff and Stefan there have been nothing but patient, helpful and cool. I can't thank those guys enough.
I reused a stock Deutsch connector to connect the bar control switches to the
wires that run back to the M-Unit inputs. I used open barrel pins and soldered after I crimped.
IMAG2207 by David Arens, on Flickr
IMAG2208 by David Arens, on Flickr
IMAG2210 by David Arens, on Flickr
Just mocking it up for length, but it's nice to be putting wire back on the bike.
IMAG2211 by David Arens, on Flickr
After studying and studying those diagrams and watching and rewatching every YouTube video on M-Unit and Harley wiring stuff I could find I set up a bench testing station to check connections before I started putting wire back on the bike.
I scanned in the stock diagram and used a free online image editing program named Gimp to cut it up into pieces. I got rid of what I didn't need and kept what I did. I created "groups" for the various circuits, Left grip switches, right grip switches, left turn signals, right turn signals and so on. I organized it into "layers" (anyone who has worked with Photoshop or other similar image editing software will be familiar with layers) so I could make changes without affecting other groups. This also makes it easy to turn visibility off and on and move groups around the page individually.
I'm planning on posting the finished diagram, but not until after everything is installed and tested. I don't want to put bad info out there. Also, even though some wire colors will be the same, this diagram will bear no resemblance to the stock one at all with regards to how things flow so it will really only be useful if you are installing an M-Unit.
I have had a couple times where I got stuck on a circuit and had to shoot an email to Revival Cycles tech line and get bailed out. Jeff and Stefan there have been nothing but patient, helpful and cool. I can't thank those guys enough.
I reused a stock Deutsch connector to connect the bar control switches to the
wires that run back to the M-Unit inputs. I used open barrel pins and soldered after I crimped.
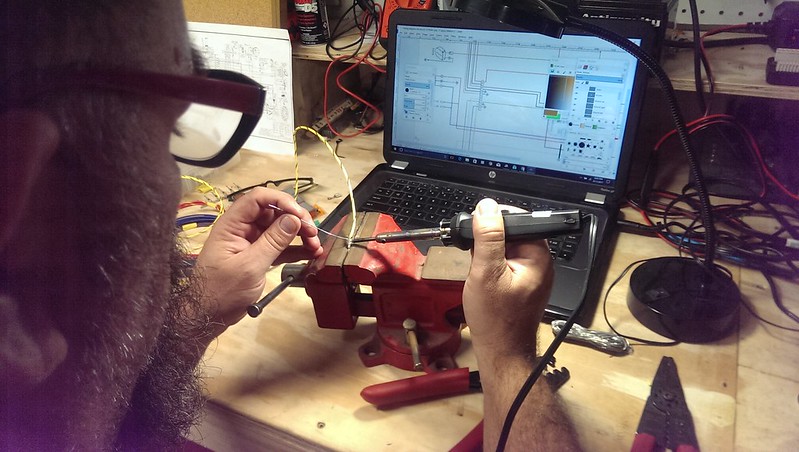
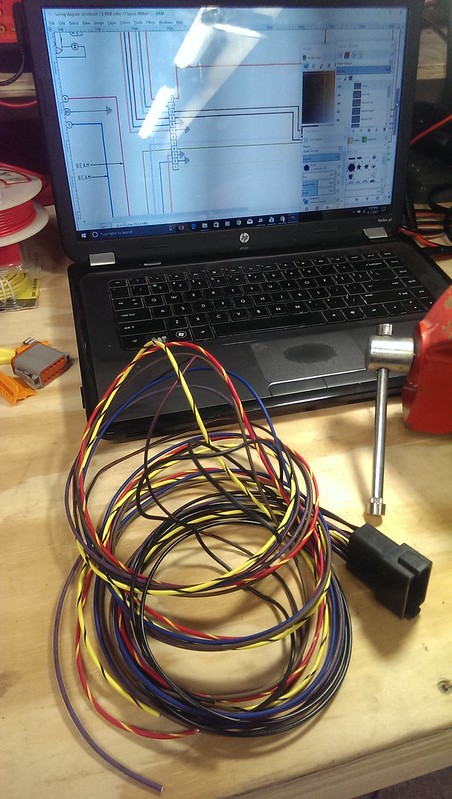
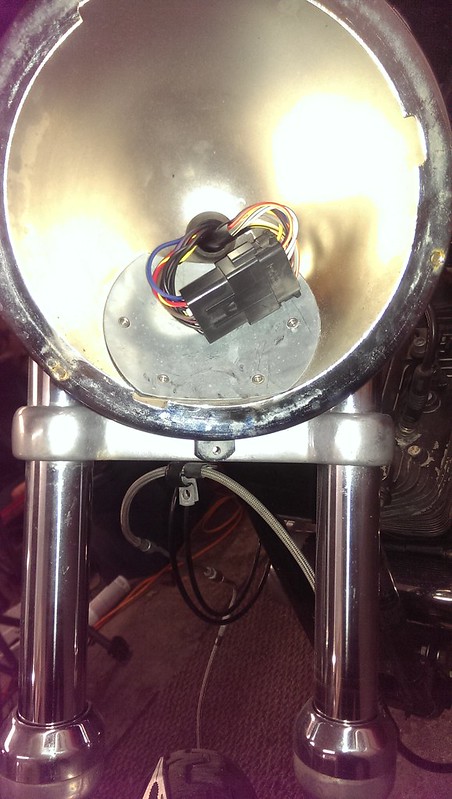
Just mocking it up for length, but it's nice to be putting wire back on the bike.
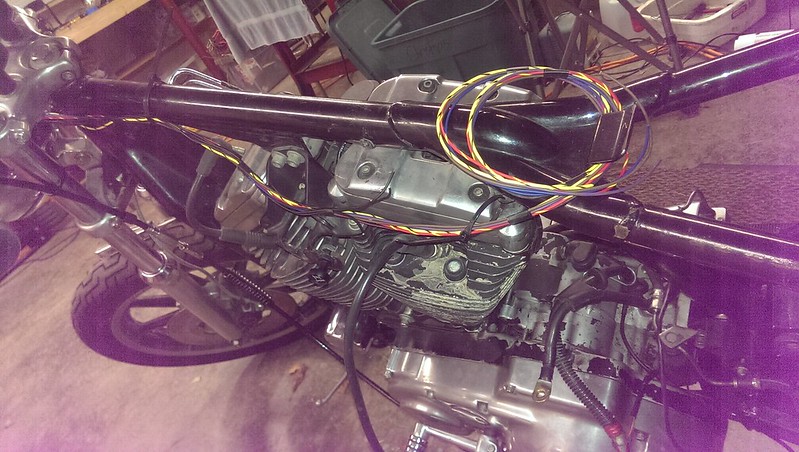
Comment